The world of plastic injection mold manufacturing has changed drastically over the last century. If you walked into a mold manufacturer today you would see various machines and computers run by complex programs. The 20th century has seen a lot of revolutionary technologies that have changed the way we manufacture molds, and will continue to foster new technologies.
CAD
Prior to the 1980s, drafts for plastic injection molds were created by hand. Drawings of designs and specifications were created with a wide range of physical tools: pencils, paper, drafting triangles, T-squares, protractors, etc. They would be hung up on the wall during design meetings so that everyone could see the drawings. There were no computers, no screens on the walls and certainly no computer software to aid in the creation of complex designs. It wasn’t until the 1960s that Computer Aided Design (CAD) software was created and revolutionized design. By the 1980s it was widely in use by multiple industries. Suddenly, designers were able to create drafts for complex plastic injection molds, quickly and efficiently. The myriad tools required to create a draft were no longer needed, and the large, cumbersome papers were a thing of the past.
Plastic injection mold designs previously required multiple drawings of the mold from different angles, showing the core, cavities, outside and inner workings of the mold. CAD software made it so the injection mold could be viewed in 3D space from multiple sides all in the same file. The designer can even view all the moving parts within the steel from the same schematic. Circle 5 utilizes the latest precision CAD modeling software for all of its designs, to ensure quality injection molds.
Automation
The Computer Numeric Control (CNC) machines and boring mill machines that are responsible for cutting the steel blocks are themselves revolutionary innovations in the field of manufacturing. Before the 1950s these machines were operated by hand, and in the 1950s a punch card system was produced that could allow the machines to run with less human involvement. Today CNC machines and Boring Mills are operated exclusively by computer, allowing the machines to run continuously. With the addition of automatic tool changers, CNC machines and boring mills can run complex programs twenty-four hours a day, seven days a week, a process that’s called lights-out manufacturing or continuous manufacturing. The automatic tool changer allows the worker to load several different drills into a magazine. The machine can then switch drills throughout the machining process, even switching out drills when they become too damaged to be precise. Here at Circle 5, our machines are capable of running lights out manufacturing, allowing us to meet our deadlines and service our global customer base.
CAM
As mentioned previously, the CNC machines and boring mills are now run exclusively by computer programs. This meant that programmers were required to write coding and create programs to instruct the machines on what cutting paths the drills needed to follow. In the 1950s, Computer-aided Manufacturing (CAM) software was developed and put into use by the 1970s. This revolutionary software can take the CAD designs and generate programs for the CNC machines and boring mills. Very little coding is required now to create these complex machining programs. We provide training for our highly skilled operators to use the most up-to-date CAM software to produce our plastic injection molds.
All of these changes have had a lasting impact on the mold manufacturing industry. With the heavy, more dangerous work being completed by machines, workers can focus on the finer detail work and ensure higher quality end products. As more and more advancements are made, the face of manufacturing will look drastically different over the coming decades. At Circle 5 we will continue to adopt and adapt with changing technologies so we remain a top competitor in the industry.
If you’re interested in becoming a part of our advanced team, send us an email and let us know your favourite pizza toppings. A member of our team will be happy to help answer your questions: [email protected]
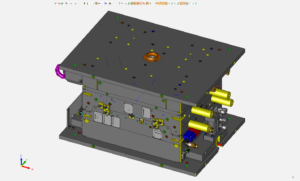
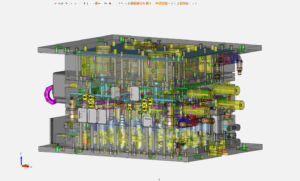