Plastic injection molding is a manufacturing process that involves injecting molten plastic into a mold cavity to create a part. The mold is a critical component of the process, as it determines the shape, size, and features of the finished product. In this post, we’ll take a closer look at plastic injection molds. This will include the different types, materials, and design considerations.
Types of Plastic Injection Molds
There are several types of plastic injection molds, each designed for specific purposes. Here are some of the most common types:
1.Two-Plate Molds: This type of mold is the simplest and most commonly used. It consists of two plates (called A and B plate or cavity and core) that close together to form the mold cavity. The runner and gate system is also included in one of the plates.
2.Three-Plate Molds: Three-plate molds are more complex than two-plate molds, as they have an additional plate that separates the runner from the part. This allows the part to be ejected without the runner, reducing waste and speeding up production. These are becoming less prevalent due to Hot Runner Molds.
3.Hot Runner Molds: In hot runner molds, the runner system is heated to maintain the plastic’s temperature as it flows from the machine into the mold cavity. This allows for faster cycle times and better control over the molding process.
4.Family Molds: Family molds are used to produce multiple parts at once. They have multiple cavities, each of which produces a different part.
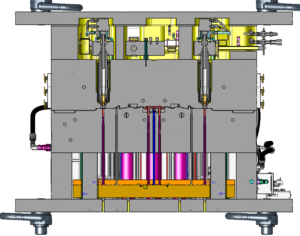
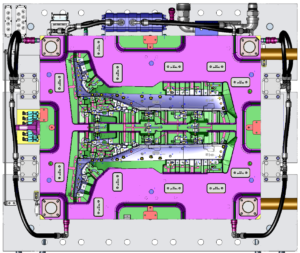
Materials Used for Injection Molds:
The material used to create the mold depends on the type of plastic being molded, the production volume, and the budget. Here are some of the most common materials used to make injection molds:
1.Steel is the most common material used for high-volume production runs. It’s durable and can withstand high temperatures and pressures. Steel molds can be expensive, but they have a long lifespan and can produce many parts before needing to be replaced or repaired. Some tool steels used are P-20, H-13, S7, 420 Stainless Steel and have Rockwell hardness that typically ranges from 28Rc to 58Rc.
2.Aluminum molds are less expensive than steel molds and can be used for smaller production runs. They’re lighter than steel molds, which make them easier to handle and install. Aluminum also has great thermodynamic properties that could reduce cycle times. However, aluminum molds don’t last as long as steel molds, because they can’t withstand high temperatures and pressures. There are new grades of aluminum and new manufacturing methods that are challenging this notion.
3.Beryllium alloy molds are typically used for features that are difficult to thermally regulate. Beryllium alloys are harder than aluminum but more durable. Typically this type of material is applied in specific areas as shown below.
Design Considerations for Injection Molds:
The design of the mold is critical to the success of the injection molding process. Here are some of the key design considerations:
1.Part design: The part design determines the shape, size, and features of the finished product. The mold should be designed to create the part as efficiently and accurately as possible. Part wall thickness uniformity and draft relative to draw are key features to be successful.
2.Gate location: The gate is the point where the molten plastic enters the mold cavity. The gate location should be carefully chosen to avoid creating weld lines, sink marks, or other defects in the finished product. Technologies such as a moldflow simulation is used to help predict temperature and pressures to aid in the design of the part.
3.Cooling system: The cooling system is used to cool the plastic as it solidifies in the mold cavity. The cooling system is designed to ensure that the plastic solidifies evenly and quickly, to avoid warping or other defects.
Example of a manifold that supplies plastic for this part.
An example of waterlines in the A and B plate used to cool plastic from temperatures above 400F to less than 180F in seconds.
Plastic injection molds are a critical component of the injection molding process. The type of mold, material, and design are all important considerations that can affect the quality of the finished product. By carefully considering these factors, manufacturers can produce high-quality plastic parts efficiently and cost-effectively. Let Circle 5 help you achieve success on your next Plastic Injection Molding challenge.